It has been hot this past month. July and August often are, but this time I wanted to do things outside after traveling all over, and what better way to beat the heat than standing in front of a 2200 F box for hours on end?
All of them. Pretty much all of the other ways are better.
So I haven’t been doing a lot, partially because I can’t seem to drink enough to keep up with the sweating over the course of three hours to avoid cramps and being a wreck the next day. But things happened!
Project 1: Bowie Knife from Farrier’s Rasp
This one’s a present for my dad, who happened to have one of his old farrier’s rasps1 laying around. Appropriate since as a little kid I used to pretend it was a sword. So after some 40 years it is time for this lucky rasp to be reborn!
And wow, a 18” knife blade is a far bigger pain in the ass than a 6” blade2. The range of ways to get the blade out of alignment, warped or otherwise just off is exponentially higher. I don’t have many pictures of the early process (or the rasp qua rasp) because I am bad at remembering pictures, but also I was constantly fixing crap.
That crack up at the tip was rather unfortunate. To be fair, I probably put it there as a kid, swinging the thing against trees. What was fortunate is that it turned up early, instead of say during heat treating. Easier to fix now.
Here’s a further shot, with the knife spending one of many days clamped to an angle iron to be heated up a bit with a torch and straightened out.
One thing to notice is the very long tang. The bottom inch or so of the rasp, and the original small tang, got turned into that. My original plan was to be cool and forge weld an iron or mild steel tang to the blade, so that the tang wouldn’t harden. The benefit there is that if you hit something a little too hard, like a tree, the tang won’t snap but will merely bend a bit. Plus it leaves more of the good, hard steel for the blade.
The problem with this is that I am not good at forge welding yet. Fortunately, I had some of the lawnmower blade left overs to experiment on first and realized it ahead of time. So now I have a long steel tang here and a badly welded knife that is just sitting around, waiting to be used on something inadvisable.
You can also notice the somewhat less than elegant tip there, where I clipped off the compromised steel. This may well turn out to be a good thing, as my father will no doubt use this for clearing a bit of brush around the place, and a stockier point moves the center of percussion (optimal striking point) a little farther towards the end. Plus it is less likely to break off, either on a sapling or my shop floor when I inevitably drop it.
Skip ahead a bit…
Here we have the roughed out knife. The bevels are now in there but largely concealed by the patina on the blade. That will of course be cleaned off, but farrier’s rasps are usually made from something like 1095 steel, and rust at the drop of a tear. I had been heating up the blade a bit to straighten out the twists (again) and when it was nearly touchable put it in the oil to cool it off and protect it a bit. Kind of a shame because you can’t see the rather neat pattern from the rasp yet.
The handle is oak, and I tried the method of fitting where you drill a small hole where you want the tang to fit, then heat the tang up a lot and stick it in the hole. The steel burns the wood out of the way and you end up with a really nice fit. I did discover that if you don’t keep it moving it will sometimes burn a bit too much near the top, so I have a little extra space to fill with epoxy, but it is overall a really handy way to go.
Then there is the hilt and pommel. That is hilt number two. I made the first one, drawing out an inch and a half of 0.5” iron, bending it, chiseling in the socket for the blade, hot forming it around the blade and tang to fit just right, got it stuck on the blade, spent a half hour taking it off during which I twisted the blade again, straightened everything again and was set, only to find that the handle was about 1/3” wider than the hilt and I couldn’t take that much off the handle without leaving gaps.
That was an exhausting moment.
I decided I wasn’t going to remake the handle, in part because I didn’t have more oak and also because it takes forever and a day to shape it, so I cut a chunk of steel out of a big flat bar I found on the side of the road and got back to work later. Later, like two weeks later. Still after all that, the new one is better (and better scaled to the knife.)
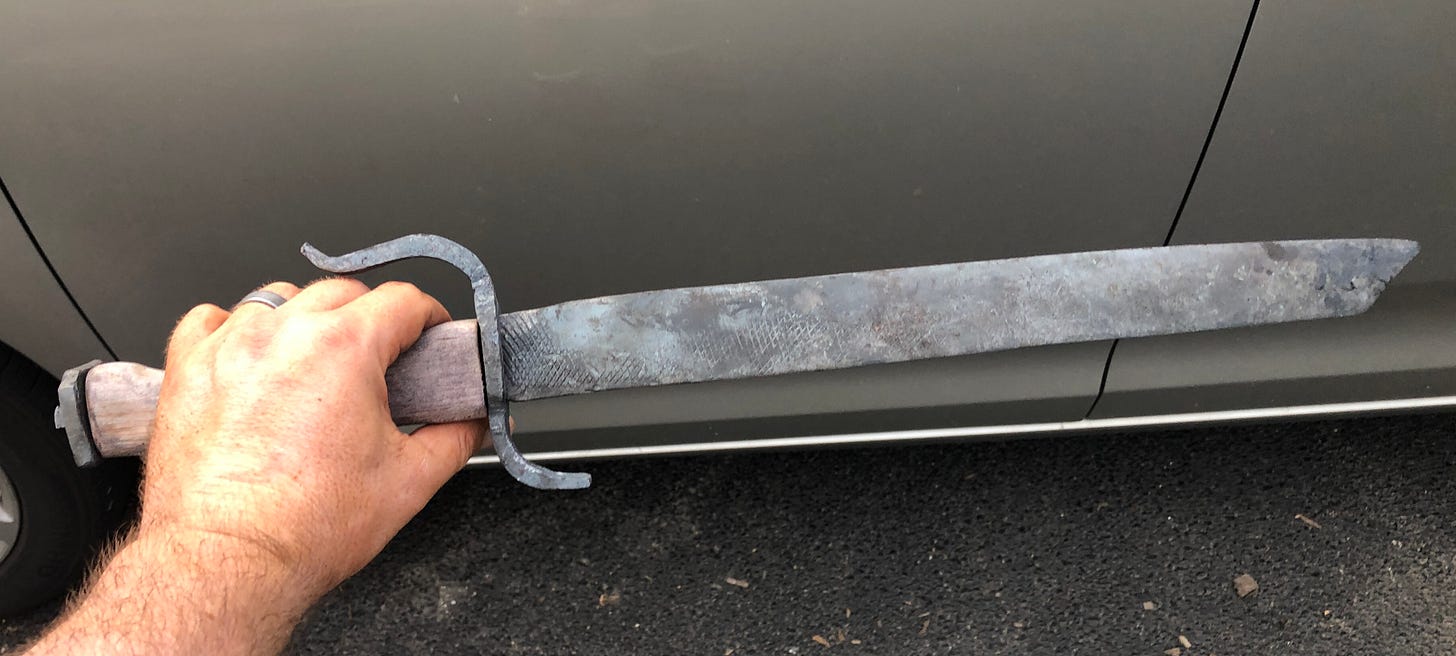
There it is sitting together. The blade still needs to be heat treated so nothing is permanent, but the hilt and handle fit together so nicely they nearly are. The pommel there is just floating; after heat treatment I will epoxy all the parts together, peen the pommel on, then do the finishing grinding, shaping and polishing on the whole thing.
Why is heat treating taking so long? Well… remember that exponential pain in the ass aspect I mentioned? I don’t have a metal container big enough to submerge an 18” blade into hot oil. Getting one is proving more irksome than I would have imagined. Apparently no stores around here carry 2-3” diameter metal pipe, it’s all pvc. So that’s a problem I need to solve, both for this project and any future sword shaped objects I build in the future.
Still, nearly there, and I am heartened that the balance and feel of the bugger is already in a pretty good spot. The point of balance is just ahead of the hilt, but I managed enough distal taper that it doesn’t handle like a crow bar, yet is solid enough that it should make a good chopper. I did that on purpose, but honestly I am a little surprised that my intentions managed to correlate with the outcome at all. Progress!
Project 2: A Fancy Knife, from Fancy Metal
It probably says something about my that I would call a basic blacksmith’s knife made from purchased steel fancy, but there you are. I mean, come on, I bought metal, online, that was actually a specific known type! Then I followed a basic set of instructions to make it instead of just fucking around and seeing what happens! I had a plan and everything!
The basic idea of a blacksmith’s knife is a utility blade with a really long and skinny tang that gets rounded back to make a handle. No wood working required. The other fun part about it is that you make it from a little bit of steel shaped kind of like a b. Draw out the round bit into a longer, thinner blade, then draw out the stem into a very long and thin bit, curl that around and hey presto, knife3!
The steel I used is from Mr. Volcano again. They sell 1.5x1/8?x12” or so bar stock of 1095 in 3 packs for 25$ on Amazon. I was also ordering an infrared thermometer to get temp readings on the forge to see if that was my problem with welding4, along with a nice set of 1/4” bolt holder tongs because, god damnit, I am not good at tongs. I would say the 25 lb package that came in the mail probably annoyed our mailman, but just a few weeks prior my wife ordered new rotors and brakes for her van online and… well if she were going to throw her back out she would have already5.
You can kind of see how the knife works there, with the long tail curled back. In fact, I didn’t draw out the blade long enough, so the whole thing sort of looks like a mouse with a long tail. Those might be called rats, I don’t know.
I probably could have drawn out the tail a bit longer too. It was looking really long when it stuck straight out, but it was just a little small for my hand.
I started with a 6” long piece, 3” of blade and 3.5” of tail, cut out of the bar such that two were made with overlapping tails. I ended up with 3.75” or so of blade. I probably should have kept working it till I had about 4-5” of blade, but I started doing the bevels too early and after that it was impossible to lengthen it without the thin parts just twisting and starting to fold over. Whoops.
Rewatching the videos, they also start out with like 5” of tail to stretch into the handle. That explains a bit too.
On the plus side, this is going to be a gift for my sister and mom, and they have little hands. It’s fine.
Run it across the angle grinder flap sander and bench grinder before the 80 grit belt sander and you get this:
Reshaping it helped me feel a bit better about the blade. In fact it is about the same size and shape of a Sanpakku knife my wife’s sister got us as a present once, so I can always claim that is what I meant to make.
But damn… I still don’t like that handle. My wife pointed out that the finger stop extending below the cutting edge made it hard to get flush with the surface, so I got out the propane torch to see what some directed burning could do.
A fair bit, as it turns out. I was able to just muscle the handle open a bit, but the torch let me heat it up to a dull red and reshape it with some pliers. Now the handle is decent for my hands, if just a tad small, but allows getting the blade flat on a cutting surface. I also wire wheeled all the random bits of scale still sticking to it.
I was so pleased with how it turned out that I wheeled out the forge and lit it up for heat treating right after.
Then, a lot of polishing later…
Note the non-stick, food safe satin finish on the handle, also known as “burned on canola oil”. I am a little nervous about the heat treat like I always am, but it holds an edge well and worked just fine for cutting up some ham I ate for dinner.
All in all I am pretty well pleased with it, although I intend to fix some of the errors with the next blank. They cook a lot, and can probably always use more knives.
This is a nice little project too: basic skills get you through, lots of good practice on those, and you don’t have any of the planning failure points I had with the big Bowie. This is the sort of thing I can see myself just knocking out for something to do on a slow day once I have my permanent shop set up. Kind of the blacksmithing version of making paper cranes, or something.
Anyway, thanks for reading!
For those who aren’t in the orbit of horse people, a farrier’s rasp is basically a really big nail file for hooves to get them shaped up nicely for shoeing, what a farrier does. They are generally made of very hard material and tend to be rather sword shaped, so that’s handy.
Insert your own joke ending in the comments below…
As usual, two good videos gave me the idea: Old Hickory Forge and Black Bear Forge.
It is not.
Our mailman is clever and uses a dolly, possibly only for our house. She at least smiles when she sees me, so she doesn’t hate us yet. I hope.
Love this. I’d be interested to read a post sometime on what goes on for you internally while doing this too. Me being currently interested in what happiness is and intuiting that this is a process you undertake not just to end up with a bit of hardware.