It’s been a bit since I talked about forging things, and there’s been a good reason for that. Well, a reason, at least: most of it hasn’t gone well. I like making stuff more than I like taking pictures of myself making stuff in general, but man, when the project itself craps out and fails it is hard to excited to share it.
But, that’s how we learn. It is also how we get really frustrated because we don’t know why it went to crap, but well, we do what we can.
First up is a project that actually worked out pretty well, which was only frustrating because it was a quick “I wonder if I can do this while I wait for more important stuff to heat up” kind of deal:
The Steel Back Shredder
A few months back I got about 200 lbs of 1-2 foot 1/2” rebar from a guy. I don’t know why he had all this in his back yard, but he did and they have little rubber ends on them and a 30 degree kink half way up, so I assume it has to do with tent or bouncy house rental? Doesn’t matter, they were free and probably untraceable, so now I have a bunch of midgrade steel to play with.
Along with a bunch of random steel I also have an itchy back, along with a strong preference for mild pain over itchiness. I was literally using the edge of a long knife to scratch my back while I work, which is pretty rough on shirts as it turns out, so a project presented itself.
Step one, draw out that rebar into a square.
Step two is to isolate the tip material by pounding in divots on two sides so that when I try to flatten the end down the material spreads out like a spoon instead of making a fan shape.
Step three is squish the tip.
I kind of feel like I should stress at this point that this wasn’t a project aiming for pretty, but more just wanting something to hit while other stuff warmed up and figuring something ugly and functional was good enough… In retrospect a fan shape probably wouldn’t look bad at all as opposed to an awkward spoon shape. Still, I need practice.1
Step four, use a chisel to split the “fingers” and round them around the bick (not pictured here. Try and polish them up a bit.
Step five, put a little hook on one end so I can hang it off shelves within reach of my desk.
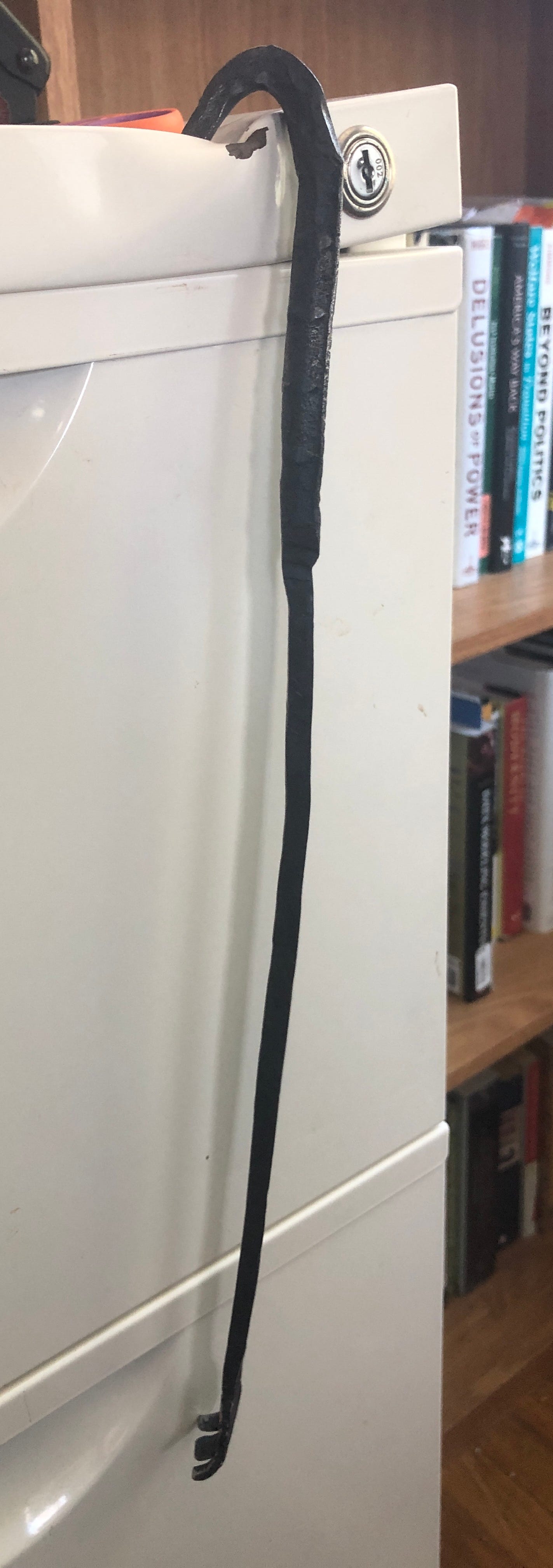
So yea, that turned out well. A little shorter than optimal, and maybe a little more aggressive than is optimal, but it gets the job done. And if I suddenly need to defend myself while in my home office it will easily cave in a skull or shatter a knee.
Can your back scratcher say the same?
Also, you can’t see it in my horrible pictures but the angles on the shank are really nice and crisp, and I didn’t do any grinding or filing work on it outside of the scratching end there (the shiny bit). Pretty pleased with how well I was able to do that with just hammer work. Of course it would look a lot better if I had carefully curved the shank while it was hot instead of testing it out, deciding it needed more curve and just bending it around the horn of the anvil cold by hand but… well I am not selling it, and I didn’t want to reheat everything.
Now… what didn’t work so well.
Bloody Knives
Ok, for the squeamish bleeding on these things is something I didn’t do at all, so don’t worry. They just aggravated me at every turn. So much so I didn’t take many pictures.
My idea was to make two good size chef’s knives. I have some 1095 steel bars I bought off Amazon about a year ago, one of which made some decent mid sized blacksmith’s knives, so I thought I would cut one in two, leaving on a little nub to forge weld a mild steel tang onto and make two good sized “I need to cleave this ham in two pieces, but I don’t want to move the knife twice” choppers.
Problems arose almost immediately as those handles you see are the second ones I had to weld on, and even those didn’t go as nicely as I had hoped. Now, forge welding is harder than most things, so much so that most knife makers avoid it like the plague and just don’t harden the steel handles, but still, aggravating that I didn’t get it right and pretty after two attempts.
The blades also really wanted to be bananas. This is always a concern when hammering in bevels on knives, especially asymmetrical single edged knives: you thin out one side and while it makes the blade wider it also wants to make that side longer, so the knife starts to curve away from the edge. Usually I can keep that under control, but eventually I broke down and said “Screw it, I’ll fix it on the grinder.”
Small aside, but in my opinion doing everything on the grinder is a bit like movie makers doing everything in post CGI. Sure, you don’t even need a forge or a hammer and anvil, you can just get a bit of bar stock and grind down everything you don’t want and put in the bevels, then use a heat treating oven. In fact, many knife makers do just that. I wouldn’t say there is anything wrong with it per se, but… well I just don’t like it. My opinion is probably wrong, but I think minimizing grind time through better forging, and forging at all, is superior, for me at least. So when I just give up and decide to grind it into shape, things have gotten bad.
Anyway, the next problem occurred with the heat treating. Now… I don’t know what went wrong here exactly. My handy heat treating reference app suggested that 1095 should be water quenched, not oil quenched. I was a little surprised but… ok, I’m game.
Well, I was game then I was mad, because the smaller knife developed fractures from the over rapid cooling. (The larger has a fracture as well, but more on that in a moment.) So that was bad, but then I cleaned off the scale and tested for hardness and… they weren’t even above 45 HRC? This was a bit of a conundrum… how are they so brittle as to crack while quenching but also that soft? And why was the app so wrong? 1095 isn’t a weird specialty alloy or something… did I not get sent 1095?
So I futzed around a bit and ground the bevels some and after a half hour or so… now they were testing at ~60 HRC, so super hard. Did the outside not harden as much as the inside? Did I somehow burn off a lot of the surface carbon so that part didn’t harden, but the inside did? Ugh… well, at least I know it did harden so I have something to work with.
But oh… since I didn’t get around to tempering them, because I thought they didn’t harden in the first place, the bigger knife developed a stress crack about an inch into the blade. Cue grumbled curses under my breath as I start tempering and decide that it will be fine and just for me to use… maybe I will cut that part down or something… need to think of a new Christmas present for my mom… grumble grumble…
So, fine. Hairline cracks aren’t the worst, and even if I don’t want to use them for food (because germs can hide in the cracks) I can at least clean them up and shape them a bit then use them for rough work. And the big one only has the one crack, and it probably isn’t that many germs compared to just having three kids… whatever.
So I did get to use my new drill press my dad got me for Christmas to put some lovely holes in the tangs, and a couple weeks ago I cut up some rhododendron wood I have around for handle scales.
So, more clean up, got the blade looking nice, put the handle scales on, pushed in the pins and…
The goddamned thing broke.
Not even at the forge welding seam, but ~1/8-1/4” in front of that in the 1095 blade. What the hell man?!
So, that’s that. At this point the whole thing is in the scrap pile, unusable until it is at least annealed and probably should just be chucked. If it had broken at the forge weld seam it would be no big deal, just another bad weld, but now I have to assume there are other stress fractures inside it that might break, and with very little warning. I mean, I was tapping brass pins in through predrilled holes and the vibration was enough to break it off. Who knows what would happen if I smacked it against a tree branch. I can only assume the other blade is similarly flawed structurally, lest I catch a big of shattered knife blade flying through the air.
So yea, a fair bit of work on two blades completely down the shitter. The only consolation prize is the practice and experience of working on them. Every little bit helps, but man, it would have been nice to get at least one knife out of it.
Stay tuned next time for “Tool Handles: Getting Good and Getting the Shaft!”
It would have been great practice for the little aspen leaf key chains I was going to make for Christmas presents, had not every single damned leaf snapped off the stem. Every single one. I was so pissed I didn’t even take a picture. That’s kind of a theme here.
Missed opportunity near the end: "Every little bit helps, but man, it would have been knife to get at least one tool out of it."