UPDATE: I have a follow up review here which is a little less positive than this one. Be sure to read that too before whipping out the credit card. I am still fairly positive about the forge kit, but less so in important ways.
As it turns out, reading, writing, deleting what I have written and starting over, and procrastinating about writing are not my only hobbies. Another set of hobbies is making stuff, and I have been meaning to get into metal working more.
Having made a coal powered foundry for melting aluminum and brass from a steel bucket, a broken lawn mower, an old vacuum and some refractory cement1 some years ago, I had a little experience making things that get appallingly hot out of inadvisably repurposed materials. I was ready to apply that knowledge to making a gas or coal powered forge from bits. Propane gas is nice because it is very clean, and for the inexperienced like me it makes controlling the heat a lot easier because you can see the piece as it heats2. Coal is nice in that it is easy to get into the place in which to burn it and doesn’t come compressed into a container that explodes if you screw up, nor does it require fancy burners and valves.
So I hopped online to see if I could find some good builds on the U-Toob, only to come across this review of a forge kit. That… was really appealing. Everything I need in one kit for a functional gas forge, and I don’t need to scrounge for parts to rivet together3? I checked out the claim that the kit was cheaper than buying the parts that it contained separately, and wow, yes it was. Oh… it’s made in America4, that’s pretty cool. And they sell a two burner version for less than twice the price?
I shopped around, looking at other options (there are a fair few), and a week later boom, a package containing a Mr. Volcano forge kit was on my porch:
Included in the kit:
Welded steel shell, with pre attached burner ports
2x Burners with ball valves and air intake chokes
Y-tubing to connect burners to standard propane grill tank
Ceramic fiber insulation
2x Fire bricks
8x bags of “Satanite” refractory cement (4 lbs total)
Bottle of rigidizer concentrate for fiber insulation
Two laminated 8.5x11” instruction sheets
Right off the bat, I have to say that full sized laminated instructions was an excellent idea. That’s the sort of little touch that says a lot about a company, in this case that the product design people knew you were going to be looking at the instructions while your hands were a filthy mess and would need durability.
Also…
As it turns out, the product is better than anticipated! Instead of having the old style ceramic fiber insulation, which needs to be hermetically sealed in refractory cement to keep it from releasing little bits of nasty that slowly kill you when it gets hot (seriously), the kit now includes a new type of fiber that refrains from launching little bits of evil into your lungs when it engages in its primary function of retaining a ton of heat! Plus, it also apparently breaks down more quickly once inside your body, as a result of, say, touching it with bare hands too much, so for those of us who have experienced having bits of fiberglass insulation making our hands itchy as all hell for weeks that is a relief. (Note: I did not test this aspect. Love of readers only goes so far.)
In fact, according to the instructions, you don’t even need the rigidizer or refractory cement anymore, because the insulation won’t kill you. They still included it, however, because the cement also keeps the insulation from getting torn to hell every time you accidentally catch it with a piece of metal. The stuff isn’t too durable by itself.
So, now that I have all these bits, it is time to put the thing together!
Step 1: Spray the rigidizer on the insulation blanket, then put it in the shell and let it dry for 24 hours.5
Note: Just assume I am writing “wear gloves to keep this crap off your skin” all the time through these steps, and maybe throw in “wear a mask”, too.
This stage requires two additional spray bottles, one >= 32 oz for the rigidizer mix (1:1 concentrate to water) and another for regular water. You mix the concentrate then spray it all over the insulation blanket till it is red, then stick it in the shell to dry. In my case, I managed to get the blanket sort of a salmon pink color.
Note: you can see the burner mount nozzles poking through the blanket there. The holes for that are pre-cut in the blanket, and line up exactly. A much appreciated point for Mr. Volcano!
One thing that bothered me a bit here is that the instructions never mention whether or not the fiber blanket needs to be compressed at all. I assumed that it didn’t, just based on my knowledge of how insulation works and figuring there needed to be airspace as much as possible. As you can see some parts naturally compressed a bit on their own more than others. I probably should have looked that up ahead of time, but I didn’t think of it till I was dripping with pink stuff and it was a bit late. Why this became an issue will be mentioned in a bit.
So then I let the stuff dry for 24 hours…. and it was still wet and soft. Then I let it dry for another 24 hours and… it was still soft, but not damp. In all fairness, it was fairly cool and damp here the week I worked on this, so that didn’t help, but that was a little troubling. I used a heat gun to get it toasty and it became a little stiffer, but not much. I did not have the gas canister to hook up and try cooking it dry, so I let it go for another day. Drying it with propane flame might have helped a lot, but as it stands I don’t know what went on there. Maybe the rigidizer doesn’t work well with the new fiber material? The instructions specify that the stuff might stay red when dry, so I am just not certain if I waited enough or should have run some fire through it.
Step 2: Mix up some Satanite Refractory Cement and smear in the first coat, then wait a few days, then smear in a second coat
The instructions recommend very carefully measuring out the cement and water. Which is fine, because the bags are not very well measured; 4 8oz bags weighed 2.25 lbs. Still, it is all close enough and so long as you get the right consistency you are probably fine. I mixed it up, got that highly desired sour cream consistency, and used a rubber spatula and my gloved hands to smooth it on in.
Three important points here:
Make sure you keep the burner sockets clear of cement. I used the handle of the scraper wrapped in a wet paper towel to periodically poke them clear. If you have very long and thin fingers they would probably do, too.
Cutting a folded piece of cardboard or thin plastic to make a smoothing tool is probably a very good idea, particularly for the bottom. The sides can be a bit rough so long as you won’t be catching bumps every time you put the piece you are working on inside, but the bottom needs to be smooth and level to allow for fire bricks to sit on an provide a flat surface. You don’t want to be heat treating a blade and pull it out only to find it is bent or twisted 5 degrees from sitting on an uneven surface.
Put some Vaseline or other grease in the little screw sockets on the burner mounts to keep cement bits from getting into the threads. I didn’t think of that the first time and had to spend a few minutes getting them clean and they still feel slightly gritty.
Again, wait 24 hours… then another 24 hours… then get frustrated and figure I have to put a second coat on anyway, so it is probably fine. I noticed a lot of pink from the rigidizer had seeped into the cement, as well. I hope that doesn’t become an issue…
Second coat goes in just like the first, only a little less material and I had a rather more solid surface to add it to. However! The air dried refractory cement is not strong enough to keep you from cracking it if you push a little. Think less “cement on rigid substrate” and more “thin candy shell on cotton candy.” This is the opportunity though to fill in all the little divots and thin spots you left the first time and cracks that formed from drying.
One other opportunity here is to make sure the refractory cement is flush with the metal shell on at least one end. One nice feature of this forge is that it is open on both sides, just a pentagonal tube, so if you wanted, say, a 32” 4 burner forge to make a broad sword, you can get another kit and hook the two together for one long forge. When doing that, however, a gap in the cement is going to result in a REALLY hot shield between the two, so the more flush the cement, the better seal you will get later. See, sometimes I do think ahead.
Then wait 24 hours. Then grumble “how many goddamned days is it really going to rain this week!?” and wait another. Then use your heat gun to get the inside toasty because you can’t believe it is still damp to the touch three days later.
Incidentally, at this point I noticed that the cement emits a lovely smell of bbq when heated. I don’t know if this is another clever touch by Mr. Volcano or the result of me having a stroke over how long everything was taking to dry, but it was very pleasant!
Step 3: Burninate the hell out of the cement to cure it into a single piece shell
Here I went pretty far off script. I still didn’t have a propane tank, so doing a series of short controlled burns to boil off the rest of the water and make the Satanite a mighty shell was not an option for a few days. Unfortunately, I was getting really impatient to play with my new toy more, so waiting was also not an option. My previous experience told me that I could burn a wood fire inside the forge to cure the refractory cement, and it would mirror the series of short burns to release steam because the heat ramps up relatively slowly.
Is this a good idea? I don’t know, but it seemed to work. The downside to not doing it slowly is that the cement can crack as the steam escapes, which is annoying but not likely fatal given the new fiber stuff. Mine didn’t crack, so I guess it worked out alright.
Well… crack more than it already was. Here’s where I was really thinking “maybe I should have smashed down that fiber”, because as I was moving the forge outside I managed to put my thumb into the cement at the top of one end and cracked the shell. After cursing a bit, I decided it was probably fine since the fiber wouldn’t kill me and it was just at the top, so it wouldn’t likely get bigger over time. It might even have served as a nice pressure release for boiling water from inside the cement shell… who knows?
I should point out though, I could totally have fixed the crack with the material in the kit! Mr. Volcano included an extra 8oz. baggie of Satanite above and beyond what you need so that you can perform future maintenance. Let me repeat that: They include extra of a product you can buy from them, because you might need some in the future for maintenance and they don’t want you to have to buy more. That’s like buying a new car and having it come with 4 extra tires, a half dozen oil filters and 5 gallons for 10w40, just to save you some trouble. Good on you, Mr. Volcano.
Then it was time to light it up!
I spent about an hour adding sticks and getting a goodly about of heat going there. Hot enough that I put a steel lid over the top and when I spit on it it bounced right off. Scientifically, that means it was hot enough to flash saliva into steam so fast that the energy released launched the rest away. Interestingly, the sides of the shell were just barely hot enough to boil away spit after a few moments. I am all about high precision measurements, obviously, but that was a really good sign that the insulation is doing its job and I hadn’t screwed anything up too badly.
After about an hour and half of cooking like that I emptied out the still yellow hot coals, carefully moved the toasty forge to its metal roll cart, and I was done!
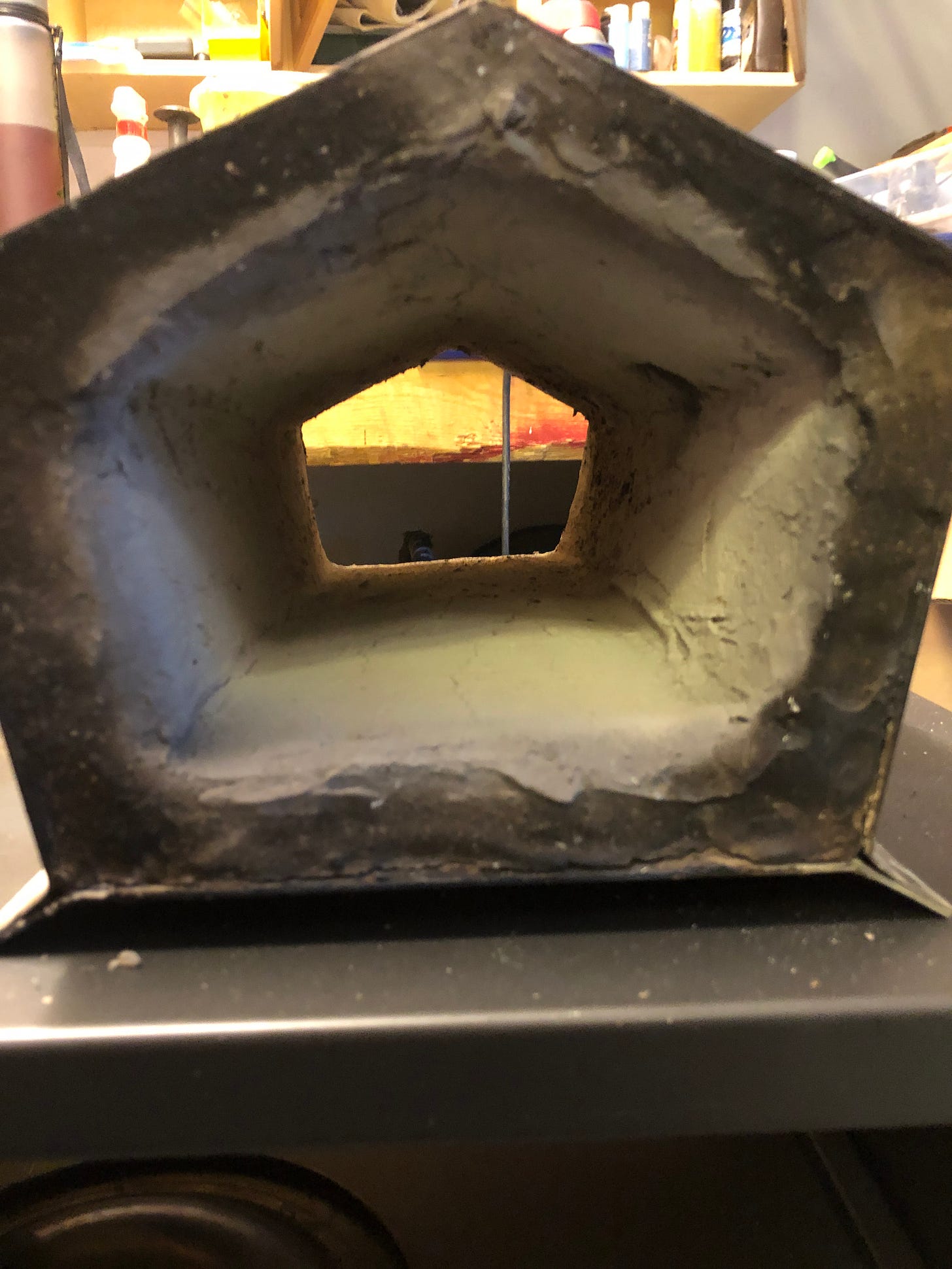
At this point, the refractory cement was rock hard, and there was no flex or give to the inside. Except where I had put my thumb in; that part has a super hard section of cement that can be pushed in on the still cushy insulation. You can just see the cracks from it at the front of the picture there6.
Next step… testing it out.
I took the bad boy outside to my sister’s place for its first test two days later, put it on some wooden round cuts, and fired it up!
I only have one burner in at the point the picture was taken. I ran both and they worked perfectly well, but I only had some small bits of steel bolt to play around with so the extra burner was unneeded. Plus I didn’t want to burn through all of my brother in law’s propane tank. I actually have no idea what the fuel consumption rate of these burners is, which I am pretty sure is never mentioned in the instructions. Still, one burner worked fine to heat up some bits for me and my nephew to play around with. (He had a good time with it!)
Another thing to note, that log in front there was damp and unburned when we started, having sat outside for months, maybe years, and being rained on every other day for the past two weeks. The heat from the front of the forge was so intense that the wood spontaneously combusted pretty quickly. I wouldn’t recommend putting this thing on your workbench without taking that into consideration.
So, would I recommend a Mr. Volcano two burner gas forge kit?
Yes, yes I would!
There are usually three aspects of a product that matter, namely:
Good quality
Cheap
Made in the USA
Typically, if you are lucky, you can pick two of those. (If you are getting a dish washer and care about number 3, that’s all you get.) This kit though nails all the points. Although exactly how much is made in the USA is questionable, you can tell the kit was designed and put together by guys who use this sort of thing and have the American customer in mind. They know what they would want in a product, and as it turns out it was pretty much exactly what I would want, too.
That said, it is important to bear in mind that I am not a professional knife maker or anything, so if this system has some problems that only an experienced user is going to spot a noob like me isn’t going to be able to report them. The video I linked above was done by a pro, however, and he seemed happy enough.
I have a few lingering doubts about how well the rigidizer worked, or how bad I screwed up application of it, but if the GOOD NEWS about the new ceramic insulation blanket is true it shouldn’t matter much. If I develop lung cancer in the next few years I will be sure to let you know before I punch my card.
All in all, I paid 135$ plus tax (free shipping) for a forge kit I couldn’t have built for the price without some serious scrounging. In fact, checking Amazon now, I might have bought the last one in existence… if I did, sorry? Mr. Volcano is still selling the single burner ones, however, and maybe the doubles will come back. Anyway, if you are like me and want to start messing around making knifes or other blacksmithy type stuff, and have a little more money than time so you don’t want to make your own gas forge from bits that might kill you, I think this is a very smart way to go. Being open ended on both sides means you can add another to get a longer forge for heat treating (because obviously you want to make a sword sooner or later), and just close off the end with some cheap fire brick when you don’t need all that space.
I should also point out that I paid for this out of pocket, didn’t get asked to write a review, anything like that. I am just excited to talk about my new toy. If you guys are interested I will post up some stories about things I make and/or grievous injuries I receive as they accumulate.
Thanks for reading!
Based on instructions found online a decade back… if I can find the link and site I will update.
I have wrecked a lot of metal burying it in the yellow hot coal of my foundry, then getting distracted for 30 seconds and leaving it in too long, resulting in pulling out a sparkler of melty metal.
Yea… I don’t even have a welder or know how to do it. I am at a 12th century tech level in a lot of ways.
Sort of; some of the parts are made in China, but the company is from Minnesota, right down the road from where I used to live there, so that’s cool.
Actual instructions available from Mr. Volcano’s site here.
Apologies for the iphone camera deciding the workbench in the background was the most important thing to focus on there… hadn’t noticed till just now.
If a sword is out of the question, I expect to see a spearhead at some point.
This is actually a really weird thing for someone else to be into. I've never really been able to actually do any forging/casting, but I spend an enormous amount of time thinking about inswool and cupola furnaces.